I finished trimming the windows, and also got some color on the wood. The window trim is basically a house style detail being a 1/2" x 2 3/4" casing, a 3/4" x 2 1/4" stool, and a 1/2" x 2 3/4" bonnet under the stool. All the reveals are a 1/4". Its a simple look, but I think its legitimate.
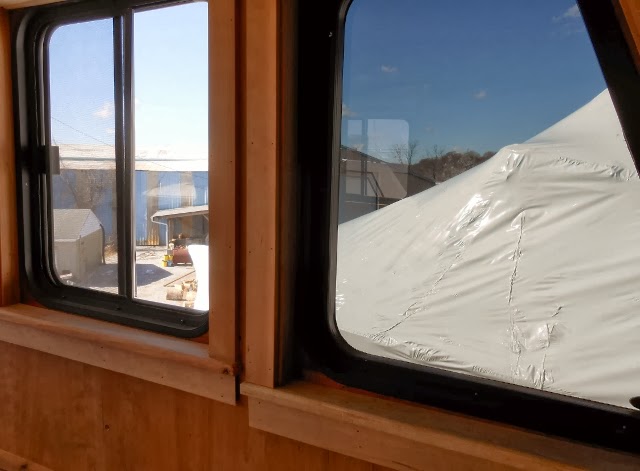.jpg)
Some more progress has been made in the wheel house, and Im inching up on getting the wood work completed. The layout was finalized, and more compromises were made. We were pretty dead set on having a 240 volt clothes drying machine and a 120 volt clothes washer, but in the end, having two units just took up too much space. In the space where the clothes dryer was going to go, I built a base cabinet with two large drawers, and two doors underneath. Because the drawers are so wide, I used 3/8 plywood for the bottoms vs the usual 1/4". Im planning on the drawers being used for paper charts and other things navigation. The drawer fronts are not installed yet as I just fitted the boxes in place.
.jpg)
.jpg)
The large opening starboard of the instrument dash area is where the electrical distribution panel is going to go. I had some sort of cut twice/measure once thing going on and screwed up the door that houses the electric panel. I found out this mistake today as I was fitting all the shiny parts Ive made in the last week.
I have the wheel house counter top fabricated and dry fitted in place, but not not yet installed. Before the top gets installed, I need to land all the wires on the bulkhead behind the distribution panel door. I used THHN for the primary wiring behind the walls, and will land all that on terminal strips. From the terminal strips, to the distribution panel, Im using a flexible, tinned, marine wire. I have about 90% of the boat wire pulled to the area under the dash, and landing it with the top off is going to be huge vs lying on my back. I realize Ill still be doing some wiring while laying down, but I want to get as much done while its relatively accessible.
.jpg)
While I was fabricating in the barn last week, I decided to make the panel that finishes covering the dry exhaust/intake stack. Because the stack is such a large fixture, I decided to make this panel a raised panel. A large, flat piece of plywood just didnt feel right. The cherry veneer plywood is for sure nice material, but in my opinion, is a little too perfect. The air dried cherry I am using oozes character, and really puts the plywood to shame in regard to interest. Being in the center of the room and such a visual element, this large raised panel looks spot on.
Heres to the coming Spring.
Cheers